19 .1 Defectología y normalización de la soldadura
Desde finales del siglo XIX se evidencia los procesos de soldadura, iniciando con la soldadura por fragua, que fue utilizada por herreros para construcción de armas y herramientas, con el paso del tiempo y el descubrimiento de las nuevas propiedades de los metales y a su vez de procesos de soldadura mucho más eficientes, que generaban una mejor unión entre dos piezas, se desarrollaron técnicas de inspección para la soldadura, con estas se buscaba hacer una evaluación y control de calidad a las piezas soldadas, a fin de asegurar que la soldadura se encontraba en perfecto estado para su uso, en otras palabras se detectaban los defectos presentes en las soldaduras.
En este documento nos centraremos en la explicación más a fondo de los defectos presentes en la soldadura, se buscara cubrir la mayor cantidad posible, explicando de manera muy detallada en que consiste y cuáles son las acciones correctivas que mejor puedan funcionar para cierto tipo de defecto.
Clasificación y cordones de soldadura
En la figura 1 se muestran los tipos de cordones de soldaduras que existen en la industria y que son los principales lugares donde se presentan los defectos.
El principal término al que se hace referencia cuando se habla de defectos de la soldadura es la discontinuidad. Esta es conocida como una interrupción en la estructura de un material que se deriva de sus propiedades mecánica, físicas entre otras, pero no necesariamente la discontinuidad sea un defecto.
Un defecto puede definirse como “Una discontinuidad o discontinuidades que por naturaleza o por efecto acumulado hacen que una parte o producto no sea capaz de satisfacer las normas o especificaciones mínimas de aceptación.”
Por tanto si tomamos en cuenta estos dos conceptos podemos definir que una soldadura defectuosa seria “Una soldadura que contenga uno o más defectos”, en el mundo de la soldadura cualquier cosa que se presente en la soldadura y sea indeseable en esta, se considerara un defecto.
Antes de empezar a hablar de cada uno de los defectos, se tiene que tener presente que también existen medidas correctivas o de mejora para dichos defectos, esto se conoce como Accion correctiva, y se puede definir como la forma de corregir algún defecto, con el fin de lograr que la soldadura pueda ser de utilizad y prestar el servicio.
Para nuestro estudio, tomaremos que los defectos están agrupados con la clasificación de la comisión V del international institute of welding. Documento IIS/IIW-340-69 donde se clasifica en 6 grupos los defectos:
- Serie 100 Fracturas: incluyendo longitudinales, transversales, radiales, en cráter, entre otras.
- Serie 200 Cavidades: Incluyendo bolsas de gas, porosidad interna, porosidad superficial, encogimiento, entre otras.
- Serie 300 Inclusiones Solidas: Incluyendo escoria, fundentes, óxidos metálicos, materiales extraños, entre otros.
- Serie 400 penetración: Incluyendo a la fusión incompleta, penetración incompleta, entre otras.
- Serie 500 Forma incompleta o contorno inaceptable: Incluyendo socavado, refuerzo excesivo, falta de llenado, forma de chaflán, traslape, entre otras.
- Serie 600 defectos varios no incluidos anteriormente: Incluyendo golpes de arco, salpicadura excesiva superficie áspera entre otros.
1. Serie 100
1.1 Fracturas: Las fracturas son la primera categoría de defectos de soldadura. Una fracturas es “Una discontinuidad del tipo de fractura caracterizada por unos bordes agudos y una gran relación entre longitud y anchura a desplazamiento de abertura” Se considera peligroso encontrar fracturas en soldaduras puesto que generan una grave reducción en la resistencia además se puede presentar una propagación de la fractura y generar una falla mucho más severa.
Las fracturas o también llamadas rupturas pueden clasificarse como
- Fracturas superficiales: Son las que se pueden observar sobre la superficie de la soldadura por medio de la inspección visual , las fracturas pueden ser longitudinales, transversales o en cráter, como las observadas en la figura 1.1 a.
Este tipo de soldadura se presenta de manera transversal, longitudinal, en cráter o en los bordes.
- Fracturas Internas o subsuperficiales: Se presentan bajo la soldadura, incluso bajo la zona afectada por el calor, muchas veces son denominadas “Bajo el cordón” como se muestra en la figura 1.1 b.
Muchas veces, estas fracturas pueden ser muy pequeñas para ser detectadas por la simple inspección visual, pero aun así no dejan de presentar un factor de riesgo, pues puede continuar expandiéndose y generar una falla del material, a este tipo de fracturas pequeñas se les denomina fisuras o si son extremadamente pequeñas micro fisuras, estas son mostradas en la figura 1.1 c.
En la siguiente tabla de la figura 1.1 c se observa algunas causas y soluciones para las grietas tanto en soldadura como en el metal base.
2. Serie 200
En la serie 200 el principal defecto son las cavidades, el tipo más común es la porosidad.
2.1 Porosidad: Esta se usa para describir los huecos globulares, libre de todo material sólido, que se encuentra con frecuencia en los cordones de soldadura. En realidad, los huecos son una forma de inclusión que resulta de las reacciones químicas que tienen lugar durante la aplicación de la soldadura. Difieren de las inclusiones de escoria en que contienen gases y no materia sólida.
Los gases que forman los huecos se derivan de los gases liberados por el enfriamiento del metal de la soldadura, como consecuencia de la reducción de solubilidad al descender la temperatura y de las reacciones químicas que tienen lugar dentro de la propia soldadura. Figura 2.1
Existen varios tipos de porosidad, algunas son las siguientes
2.2 Porosidad dispersa: Esta uniformemente distribuida a través del metal duro.Figura 2.2
2.3 Porosidad agrupada: Es un arreglo localizado que tiene una distribución geométrica al azar. Figura 2.3
2.4 Porosidad alargada: Es aquella porosidad cuya longitud es mayor a su ancho y se ubica aproximadamente paralelas al eje de la soldadura. Se puede formar en el interior o en la superficie del metal de soldadura. Figura 2.4
2.5 Porosidad superficial, en el cráter y de gusano: Es fácilmente observable por medio de la inspección visual. Figura 2.5
Es importante resaltar que la porosidad no es un defecto tan serio como las fracturas, esto se debe principalmente a que las cavidades de porosidad presentan extremos redondos y no se propagan como sucede con las fracturas. Algunos códigos proporcionan diagramas de comparación que muestran la cantidad aceptable de porosidad que se puede presentar en las soldaduras. El siguiente diagrama mostrado en la figura 2.6 es el usado en el código 1104 API.
En el siguiente cuadro se observan posibles causas, corrección y responsabilidades que generan que en los procesos de soldadura se presenten cavidades.
3. Serie 300
La serie 300 del documento IIW explica un tipo de defecto llamado inclusiones sólidas, estas en el mayor de los casos se consideran un defecto subsuperficial o interno, es decir no puede ser detectado fácilmente por inspección visual, se necesita recurrir a los ensayos con tintas penetrantes, radiografías o ultrasonido que permita detectar este tipo de defecto.
3 .1 Inclusiones no Metálicas: Son los óxidos no metálicos que se encuentran a veces en forma de inclusiones alargadas y globulares en los cordones de soldadura. Durante la formación del depósito y la subsecuente solidificación del metal de la soldadura, tienen lugar muchas reacciones químicas entre los materiales (fundente), o con la escoria producida. Algunos de los productos de dichas reacciones son compuestos no metálicos, solubles solo en cierto grado en el metal fundido. Debido a su menor densidad, tienden a buscar la superficie exterior del metal fundido, salvo que encuentren restricciones para ello, en la figura 3.1 se muestra una inclusión de escoria en un cordón de la soldadura.
3.2 Inclusiones alineadas: Se presenta paralelas al eje de soldadura y se presentan de manera interna en esta. Figura 3.2
Uno de los principales materiales usados en la soldadura, especialmente en la TIG es el tungsteno, muchas veces, este material puede quedar como escoria en el cordón, la siguiente imagen es de inclusiones de tungsteno, estas inclusiones no se pueden detectar mediante técnicas de inspección interna, en especial la radiografía. La figura 3.3 muestra inclusiones de tungsteno en un cordón de soldadura.
En general, las inclusiones de fundente o de escoria son redondas y no poseen esquinas agudas como las fracturas y por estas razones no son tan peligrosas como las fracturas.
En algunos metales, particularmente en lo que se presenta recubrimientos térmicos de óxido, hay posibilidades de inclusión de óxido en el metal de soldadura. Este problema se vuelve grave principalmente cuando se suelda aluminio, puesto que el óxido de aluminio se forma rápidamente en el atmósfera y puede quedar atrapado muy fácilmente en el metal de soldadura si no se toman precauciones o no se hace limpieza.
En el siguiente cuadro figura 3.4 se observan posibles causas, corrección y responsabilidades que generan que en los procesos de soldadura se presenten inclusiones.
4. Serie 400
La serie 400 del documento nos centra en los defectos generados por fusión o penetración incompleta.
4.1 Fusión Incompleta: Un defecto conocido como carencia de fusión es simplemente una gota de soldadura en la cual no ocurre la fusión a través de toda la sección transversal del al unión. Es decir la soldadura depositada no lleno completamente la preparación de la unión o que hay un espacio entre los cordones o pasos, o un espacio en la raíz de la unión.
Uno de los principales problemas es la producción de esfuerzos y tensiones a raíz de este defecto. En la figura 4.1 se muestra un cordón con fusión incompleta y un esquema del defecto.
4.2 Penetración incompleta: Esta expresión se usa para describir la situación en que el metal depositado y el metal base no se funden en forma integral en la raíz de la soldadura. Puede ser ocasionada porque la cara de la raíz de la soldadura de ranura no alcance la temperatura de fusión a toda su altura, o porque el metal de la soldadura no llegue a la raíz de una soldadura de filete, y deje el hueco ocasionado por el puenteo del metal de la soldadura desde un miembro al otro.
Aunque la penetración incompleta puede deberse en unos cuantos casos a la falta de disolución de los óxidos e impurezas de la superficie, las condiciones de transmisión de calor que existen en la junta son una fuente más frecuente de este defecto. En la figura 4.2a se observa esquemas de juntas con penetración incompleta.
La penetración incompleta es indeseable, particularmente si la raíz de la soldadura está sujeta ya sea a tensión directa o a esfuerzos flexionantes. El área que no se funde permite concentraciones de esfuerzos que pueden resultar en fallas sin deformación apreciable.
La figura 4.2 c muestra falta de penetración pero por efecto de des alineamiento en el cordón de soldadura.
En el siguiente cuadro figura 4.3 se observan posibles causas, corrección y responsabilidades que generan que en los procesos de soldadura se presenten Fusión incompleta.
5. Serie 500
Los defectos tratados en esta parte del documento son las formas imperfectas o contornos inaceptables, uno de los principales defectos en esta sección es el socavado o socavamiento.
5.1 Socavamiento: Se emplea este término para describir:
- La eliminación por fusión de la pared de una ranura de soldadura en el borde de una capa o cordón, con la formación de una depresión marcada en la pared lateral en la zona a la que debe unirse por fusión la siguiente capa o cordón.
- La reducción de espesor en el metal base, en la línea en la que se unió por fusión el último cordón de la superficie.
El socavamiento en ambos casos se debe a la técnica empleada por el operador. Ciertos electrodos, una corriente demasiado alta, o un arco demasiado largo, pueden aumentar la tendencia al socavamiento.
Los principales problemas que genera el socavado son que producen un amplificador de esfuerzos que causan problemas cuando hay impacto o fatiga en la estructura y también el servicio a bajas temperaturas.
La figura 5.1 a muestra un esquema y a su vez una pieza con defectos de socavamiento.
Puesto que la serie 500 trata las formas imperfectas algunas de ellas son las mostradas en la figura 5.1 b y que representan un defecto para la soldaduras
En el siguiente cuadro. Figura 5.2 se observan posibles causas, corrección y responsabilidades que generan que en los procesos de soldadura se presenten socavados.
6. Serie 600
Los defectos varios son la última categoría que se observa en la norma.
En la categoría de diversos están los golpes de arco ( Figura 6.1 a ) en los cuales el soldador accidentalmente permite que el electrodo toque el metal base junto a la unión dejando una cicatriz en la parte; la salpicadura excesiva (Figura 6.1 b) en la cual caen gotas del metal de soldadura fundido en la superficie de las partes base; y otros defectos no incluidos en las categorías anteriores
En el siguiente cuadro. Figura 6.2 se observan posibles causas, corrección y responsabilidades que generan que en los procesos de soldadura se presenten defectos varios.
En el siguiente vídeo se observa algunos de los defectos explicados anteriormente, el vídeo se basa en la soldadura MIG y MAG.
DEFECTOS Y SOLUCIONES EN EL PROCESO DE SOLDADURA MIG/MAG
En el siguiente vídeo se observan también varios defectos de la soldadura y algunas técnicas para detectar dichos defectos.
DEFECTOS Y METODOS DE INSPECCION NO DESTRUCTIVA PARA UNIONES DE SOLDADURA.
Para finalizar, resta decir que los defectos que se presentan en la soldadura son muchos, incluso algunos más a los mencionados, se presentan de diversas formas y cada uno de ellos como se explicó se genera por causas distintas, genera problemas distintos en las piezas donde son soldadas, también se detectan de distintas maneras, por eso es tan importante el profundo conocimiento de estos problemas y que sea un profesional quien evalué y haga un control de calidad a la soldadura para evitar problemas a futuro y que se garantice el correcto funcionamiento de la soldadura.
Para una mayor información sobre los defectos se pueden consultas las normas:
- ANSI –(American National Standards Institute)
- ACI –(American National Standards Institute)
- AWS –(American Welding Society)
- ASME –(American Society of Mechanical Engineers)
19.2 Simbología y normalización de la soldadura
La simbología de soldadura nos proporciona un conjunto de información que acompaña a un plano de una construcción metal-mecánica con trabajos de soldadura, implica una serie de símbolos y referencias alfa numéricas (letras y números) ubicada en lugares particulares de los respectivos planos. La simbología y el respectivo detalle escrito proporcionan la información necesaria para ejecutar el trabajo de soldadura en las condiciones en que se pensó a la hora del diseño. El hecho de que la soldadura se realice como se diseñó dependerá del nivel de detalle que se indique en el plano, que finalmente es lo que llega a quien realiza el trabajo o lo coordina y podrá en base a la simbología dar las indicaciones correspondientes.
El empleo correcto de estos símbolos requiere el conocimiento de los mismos y la regla asociadas con su construcción, uso e interpretación. Por otra parte, existen varios tipos de soldadura (y sus respectivos símbolos) e innumerables situaciones de aplicación de cada tipo, por lo que para ampliar sobre este tema pueden remitirse a la norma o a la parte de la norma que resulte de interés.
1. Símbolos básicos
1.1 Símbolos de soldadura y símbolos de soldeo: En esta norma se hace distinción entre los términos símbolo de soldadura y símbolo de soldeo. El símbolo de soldadura indica el tipo de soldadura y, cuando se utilice, forma parte del símbolo de soldeo. Los símbolos de soldadura serán como los indicados en la Figura 1.1.a los símbolos se representan sobre la línea de referencia (indicada a trazos con fines ilustrativos), y los símbolos de soldeo están constituidos por varios elementos, los únicos elementos requeridos son la línea de referencia y la flecha, los elementos adicionales pueden incluirse para facilitar la información de soldeo específica, todos los elementos cuando se utilicen estarán en posiciones especificas del símbolo de soldeo como se indica en la Figura 1.1.b
1.2 Símbolos suplementarios: teniendo en cuenta la situación del símbolo de soldeo la flecha debe señalar a una línea del plano que identifique de forma univoca la unión en cuestión, se recomienda que la flecha señale una línea continua, sin embargo, la flecha puede señalar a una línea discontinua. Los símbolos suplementarios que se utilicen conjuntamente con los símbolos de soldeo se indicaran como se muestra en la Figura 1.2
2. Tipos básicos de uniones
Los tipos básicos de uniones se muestran en la figura 2.
3. Consideraciones generales
3.1 Significado de la posición de la flecha: La información aplicable al lado de la flecha de una unión se situara por debajo de la línea de referencia, la información aplicable al otro lado de la unión se situara por encima de la línea de referencia como se muestra en la figura 3.1.
3.2 Ubicación de la soldadura en la junta, según posición del símbolo en línea de referencia:
a. La soldadura se aplicará al lado del punto de contacto de la flecha si el símbolo de soldadura está en la parte inferior de la línea de referencia como se muestra en la figura 3.2.a.
b. La soldadura se aplicará al lado opuesto del punto de contacto de la flecha si el símbolo de soldadura está en la parte superior de la línea de referencia como se muestra en la figura 3.2.b.
c. La soldadura se aplicará en ambos lados, de la unión, cuando los símbolos aparecen en ambos lados de la línea horizontal de referencia como se muestra en la figura 3.2.c. Si la línea de referencia horizontal tiene símbolos en ambos lados, un símbolo puede ser distinto al otro, o sea, las dos soldaduras tendrán formas distintas.
3.3 Información ubicada en la cola de la línea de referencia: La cola, de la línea de referencia, es utilizada para ubicar información como: procedimientos, tipo de proceso, especificaciones, tipo de metal de aporte, necesidad de limpieza de la raíz, referencia a otros detalles del plano, etc, ver figura 3.3.
En los cuadros siguientes, se muestran las diferentes letras que identifican los procesos con sus variaciones que se deben colocar en la cola de la línea, según el caso especifico
4. Descripción de símbolos suplementarios
4.1 Símbolo de soldadura de respaldo: Se aplica en numerosos tipos de soldadura para describir que la penetración va más allá de la superficie de respaldo de la unión. El símbolo de refuerzo siempre aparece relleno de negro. El relleno puede ir dimensionado a la izquierda del símbolo como se ve en la figura 4.1.
4.2 Soldadura de contorno: La soldadura se aplica alrededor de la pieza. Ver figura 4.2
4.3 Línea quebrada: Las línea de referencia quebrada, indica que la junta que se debe preparar (biselar, achaflanar, etc.), es la señalada en la dirección de la flecha como se muestra en la figura 4.3.a. y 4.3.b.
4.4 Símbolos de soldadura combinado: En las uniones que requieren más de un tipo de soldadura, se utilizara un símbolo para especificar cada soldadura como se muestra en la figura 4.4.
4.5 Líneas de flechas múltiples: Dos o más flechas pueden ser utilizadas con una única línea de referencia para señalar las posiciones donde se especifican soldaduras idénticas como se muestra en la figura 4.5.
4.6 Múltiples líneas de referencia: Se utilizan para señalar secuencias de operaciones, la primera operación se especifica en la línea de referencia más cercana a la flecha como en la figura 4.6, las posteriores operaciones se especifican secuencialmente.
4.7 Tolerancia de la dimensión de la soldadura: Cuando una tolerancia sea aplicable a la dimensión de un símbolo de soldadura, se indicara en la cola del símbolo con referencia a la dimensión a la que aplique como se muestra en la figura 4.7, o la tolerancia se especificara mediante una nota de plano
5. Dimensionamiento y representación de la soldadura en soldadura de filete
Este tipo de soldadura (soldeo) es el más común y su aspecto recuerda a un triángulo que resulta de unir dos superficies en ángulo como los casos de las soldaduras en “t”, en solapa y en esquina. La soldadura en filete posiblemente represente el 80% de todas las uniones soldadas por arco eléctrico
5.1 Terminología de una unión soldada en filete, figura 5.1.
5.2 Dimensiones de la soldadura de filete: Las medidas de altura y ancho del filete se ubican a la izquierda del símbolo. La medida del extremo izquierdo es la altura. La longitud del filete y la distancia entre centros de intervalos de soldadura se colocan a la derecha del símbolo. La primera medida, de la derecha del símbolo, corresponde a la longitud del filete; luego, va un guion que separa la medida entre centros de intervalos.
Una práctica común es la aplicación de soldadura en intervalos intermitentes, en lugar de continua, para disminuir la tensión y la distorsión entre los materiales. Así mismo, para ahorrar material y tiempo en la aplicación de la soldadura, si a la derecha no hay dimensión, implica que la soldadura es continua a lo largo de toda la unión, ver figuras 5.2.a y 5.2.b.
5.3 Ubicación de las medidas: Si las dimensiones y características del filete es la misma en todas las piezas del dibujo, no es necesario colocar símbolos en cada soldadura. Mejor se coloca un solo símbolo con una nota general para todas las soldaduras del dibujo como lo muestra la figura 5.3. En caso contrario, cada soldadura debe acompañarse de su símbolo con sus respectivas dimensiones.
5.4 Dirección de la soldadura: La dirección y ubicaciones de los cordones localizados de la soldadura se especifican con esquemas como se muestra en la figura 5.4
5.5 Representación de la forma de acabado de superficie: Representación del contorno o forma de acabado del filete: Convexo, cóncavo, liso etc, ver figura 5.5.
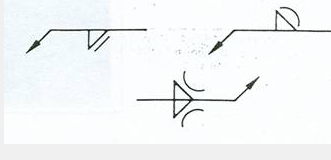
1.1. Representación de la forma de acabado de superficie: Representación del contorno o forma de acabado del filete: Convexo, cóncavo, liso etc.
6. Símbolos de exámenes no destructivos
Los métodos de exámenes no destructivos se especifican utilizando las letras de designación que se indican a continuación en la figura 6.
6.1 Situación normalizada de los elementos de un símbolo de examen no destructivo: los elementos de un símbolo de examen no destructivo tendrán situaciones normalizadas entre ellos como se indica en la figura 6.1.
[1] Universidad Tecnológica de Pereira (2010: Colombia), http://www.utp.edu.co/~azapata/simbologia.htm [Consulta: miércoles, 2 de diciembre de 2015].
[2] Coordinación de comunicación de proyectos de diseños industriales (24 agosto, 2014), https://diuanl.files.wordpress.com/2012/08/simbolos-de-soldadura.pdf [Consulta: miércoles, 2 de diciembre de 2015].
[3] Símbolos normalizados para soldeo, soldeo fuerte y examen no destructivo (Aprobado por instituto de normalización nacional americano 19 de junio de 1991) Traducción de una norma nacional americana ANSI/AWSA2.4-93, sustituye a ANSI/AWS A.2.4-86 [Consulta: miércoles, 2 de diciembre de 2015].
[4] Universidad Católica del Norte (2010: Chile), http://www3.ucn.cl/FacultadesInstitutos/laboratorio/Defectosm6.htm [Consulta: miércoles, 2 de diciembre de 2015].
[5] slideshare.net (2014: E.E.U.U), http://es.slideshare.net/marcus1910/discontinuidaes-y-defectos-en-soldadura-29694095 [Consulta: miércoles, 2 de diciembre de 2015].
[6]Presentaciones Power Point de las conferencias realizadas en el IV CBIME, http://es.slideshare.net/xMorfe0x/2-acciones-correctivas-para-defectos-de-soldadura [Consulta: Viernes, 11 de diciembre de 2015].
[7] Solución integral en unión y corte de materiales SOLDADURAS WEST ARCO, soporte, http://www.westarco.com/westarco/sp/soporte/defectos_soldadura_causa_soluciones.cfm [Consulta: Viernes, 11 de diciembre de 2015].
[8] InstitutoAsteco, Defectos y soluciones en el proceso de soldadura MIG/MAG, https://www.youtube.com/watch?v=lLtTGcf380I, [Consulta: miércoles, 2 de diciembre de 2015].
[9] Defectos y métodos de inspección no destructiva para uniones soldadas, https://www.youtube.com/watch?v=PoNd5cHUDjc, [Consulta: miércoles, 2 de diciembre de 2015].
[10] Evaluación y control de calidad de la soldadura, fotocopias profesor José Albeniz Hurtado Cardona, Universidad Tecnológica de Pereira. [Consulta: Viernes, 27 de diciembre de 2015].
Información recopilada por:
Daniel Felipe Grajales Martinez
Alejandro Martinez Arias